在特斯拉宣布一體壓鑄技術(shù)取得新突破之后,全球銷冠汽車公司豐田近日也公開了其開發(fā)的車身一體壓鑄成型技術(shù)。豐田表示,該技術(shù)旨在進(jìn)一步降低生產(chǎn)工序和成本,從而在難以通過傳統(tǒng)制造方式盈利的電動車領(lǐng)域提高利潤。
據(jù)豐田方面介紹,在使用一體壓鑄技術(shù)之前,一個完整的車身后部需要約86個不同的零部件,并且需要經(jīng)過33個獨(dú)立的工序來組裝。這一復(fù)雜的過程通常需要數(shù)小時來完成,在應(yīng)用一體壓鑄工藝后,車身后部只需一個單一的零部件和一個簡單的工序。豐田計劃進(jìn)一步縮短時間,將工序縮短至約3分鐘。
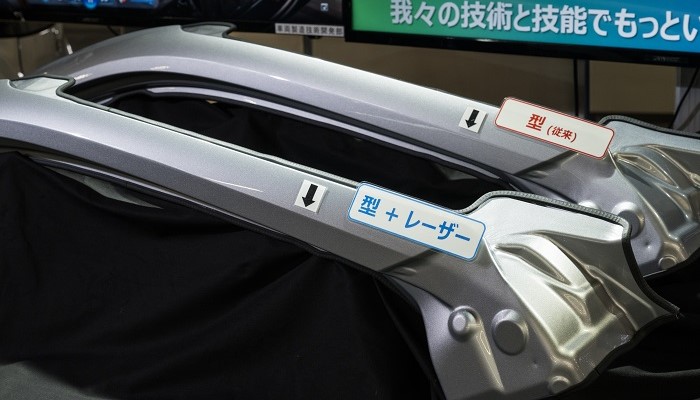
該技術(shù)在結(jié)構(gòu)更加復(fù)雜的車身前部提升更加明顯——豐田表示,傳統(tǒng)的制造方法需要用到91個零部件,并且要經(jīng)過51個工序。而使用一體壓鑄技術(shù)后,零部件和工序同樣可以簡化為一個單一的零部件和一個工序。
這一制造流程進(jìn)步盡管相較傳統(tǒng)流程已經(jīng)具有明顯進(jìn)步,但仍落后于特斯拉。據(jù)特斯拉最新曝光的一體壓鑄工藝相關(guān)信息顯示,目前特斯拉已經(jīng)具備將幾乎所有車身底部零部件整合壓鑄,這將幫助特斯拉再次減半其生產(chǎn)成本。
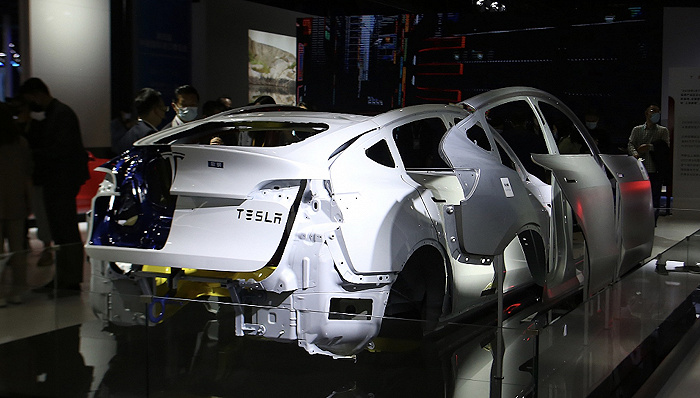
另一方面,通過在測試模具上使用3D打印機(jī),特斯拉同樣在車輛開發(fā)領(lǐng)域具備成本優(yōu)勢。相關(guān)消息人士表示,通過在設(shè)計驗(yàn)證領(lǐng)域應(yīng)用該方法,可使模型成本降低至傳統(tǒng)金屬模型的僅3%。
為盡量加快抹平特斯拉在制造成本方面取得的優(yōu)勢,豐田同時改變了其生產(chǎn)方式。在豐田愛知本町工廠,豐田部分實(shí)施了一種不依賴傳送帶的生產(chǎn)方式。
據(jù)豐田介紹,完成組裝的車輛在工廠內(nèi)通過傳感器識別和有限自動駕駛技術(shù)來完成點(diǎn)到點(diǎn)的運(yùn)輸。這在降低產(chǎn)線投資的同時,也使得豐田能夠在短時間內(nèi)變更其工廠內(nèi)部配置。
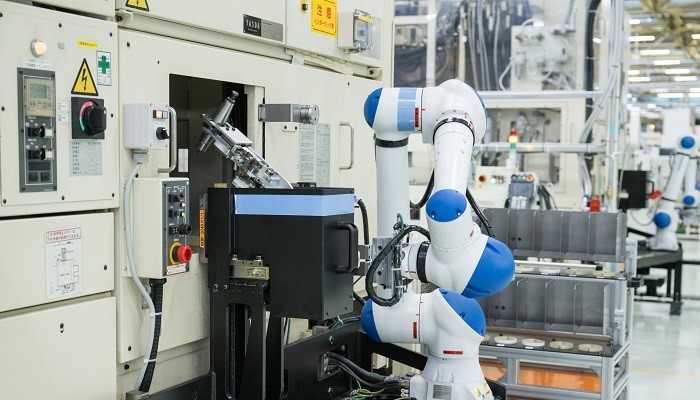
經(jīng)過對電動化轉(zhuǎn)型舉棋不定的十年后,豐田正在加速追趕特斯拉的腳步。除領(lǐng)近期曝光的生產(chǎn)工藝改良和一體化壓鑄工藝的應(yīng)用,豐田在今年7月公布了對固態(tài)電池的重大技術(shù)突破;此外,通過對生成式AI技術(shù)的應(yīng)用,豐田有望在車型開發(fā)過程中加快工作效率。
數(shù)據(jù)顯示,特斯拉2022年的全球銷量約131萬輛,而豐田純電動車的銷量僅為2.4萬輛。不過,在對電池技術(shù)完成突破、應(yīng)用AI、一體壓鑄和自動駕駛等技術(shù)后,豐田希望快速追趕特斯拉的銷量——該公司希望到2026年完成純電車型年銷150萬輛的成績,這一數(shù)字是2022年銷量的60倍以上。